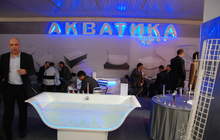
В связи с переоборудованием на производственном предприятии холдинга Акватика, в ноябре 2004г. внедрена новая многоступенчатая система контроля качества.
Основными составляющими новой системы качества являются:
1.Ежемесячный анализ по выпускаемой продукции с указанием процента брака и причин его возникновения на основе статистики, получаемой от оптовых клиентов, розничных покупателей, авторизованного сервисного центра.
2.Введение личных номеров всем сотрудникам, принимающих участие в непосредственном выпуске продукции и полной материальной ответственности всего персонала предприятия.
3.100% проверка изделий, выпущенных заводом на специальных стендах и при работе на всех режимах.
Что такое новая многоступенчатая система качества?
В настоящее время осуществляется промежуточный контроль 100% изделий на всех технологических этапах. Контроль качества начинается с поступления на склад сырья, комплектующих и расходных материалов. Результатом является акт входного контроля на соответствие их международным требованиям и стандартам.
Поэтапный контроль после каждой технологической операции включает в себя следующие операции:
Контроль после операции термовакуумная формовка. Осуществляется визуальный осмотр изделия-заготовки на наличие раковин, сколов, инородных вкраплений и т.д. Изделие проверяется на наличие отклонений по допускам в геометрических размерах, кривизне и толщине акрилового слоя. На изделие (заготовки), прошедшее проверку оформляется внутризаводской паспорт с присвоением заводского номера. Изделия (заготовки), не прошедшие контроль, актируются и подлежат уничтожению
Контроль операции армирования. Осуществляется визуальный контроль качества нанесения армирующего слоя Термоблок. По специальной методике проверяются адгезионные свойства армирующего слоя. С помощью шаблонов и приспособлений проверяются плоскости изделий на наличие деформаций, возникновение которых возможно в процессе усадок материалов. Контроль допусков производится по утвержденным номиналам.
Контроль операции обрезки. Фасонная обрезка сложных изделий производится вручную высококвалифицированными специалистами по шаблонам. Проверка шаблонов и их аттестация проводится начальником ОТК не реже 1-го раза в 3 месяца. Обрезка по горизонтальной плоскости производится на обрезочном комплексе. После завершения операции контролируются следующие параметры: место входа-выхода режущего инструмента для горизонтальной обрезки – прямолинейность обрезки, ровная высота бортов, для фасонной обрезки – соответствие шаблону контроль всех плоскостей среза производится специальным инструментом, гостируемым не реже 1 раза в 3 месяца Порядок дефектации продукции такой же, как на операции термовакуумной формовки.
Контрольное тестирование гидромассажных ванн. Осуществляется по производственным инструкциям с утвержденным регламентом. Испытания производятся на специальном стенде по ТУ 4941-001-54876088-03. Каждое испытываемое изделие тестируется в полном рабочем режиме не менее 60 мин. Результатом приемки является внесение записей и отметок в контрольной карте, а также штамп выходного контроля в техническом паспорте изделия.
Выходной контроль изделия. Осуществляет начальник службы ОТК по производственной инструкции. Контролируемые параметры определяются утвержденными номиналами на изделия и являются стандартом предприятия. Данная система качества позволяет вести статистику по рекламациям, быстро и безошибочно определять участки и ответственных за допущение брака, своевременно выводить из производства изделия с отклонениями от ТУ. Все это позволяет анализировать нашу работу, искать новые пути, методы дальнейшего совершенствования качества.